I have three electrics hanging from 2001 vintage JR Clancy winches-- the drill-drive, single haul line kind with no built-in fail safe... When I look inside the drums through an empty cable inlet, two of them look nice and clean, and the third one has a bunch of rust all over. Pictures below.
I have two ideas in my head:
1. There is a lot of good steel there still and this probably isn't the weakest link in the whole assembly.
2. Rusted components in overhead rigging should be removed from service.
What would you do? Unload the electric and tag it out until replacement? Not worry so much and just plan to replace all three some year soon because they're just generally sketchy? Spray rust inhibitor inside, give it a spin and pretend it never happened (sort of joking)?



I have two ideas in my head:
1. There is a lot of good steel there still and this probably isn't the weakest link in the whole assembly.
2. Rusted components in overhead rigging should be removed from service.
What would you do? Unload the electric and tag it out until replacement? Not worry so much and just plan to replace all three some year soon because they're just generally sketchy? Spray rust inhibitor inside, give it a spin and pretend it never happened (sort of joking)?
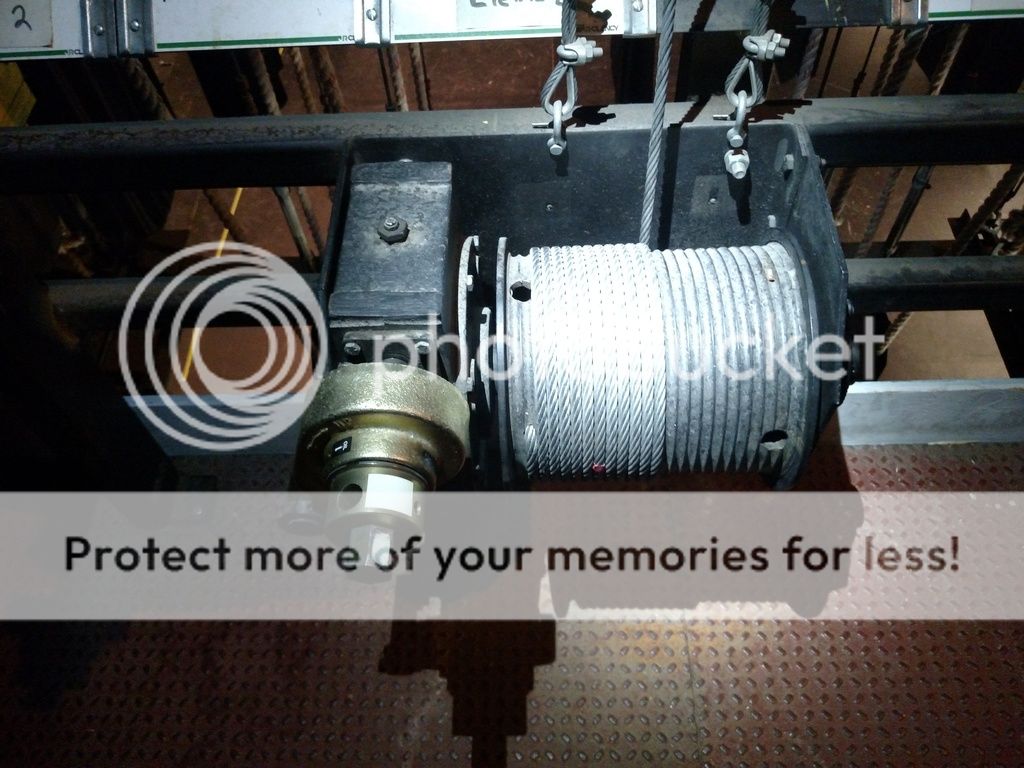
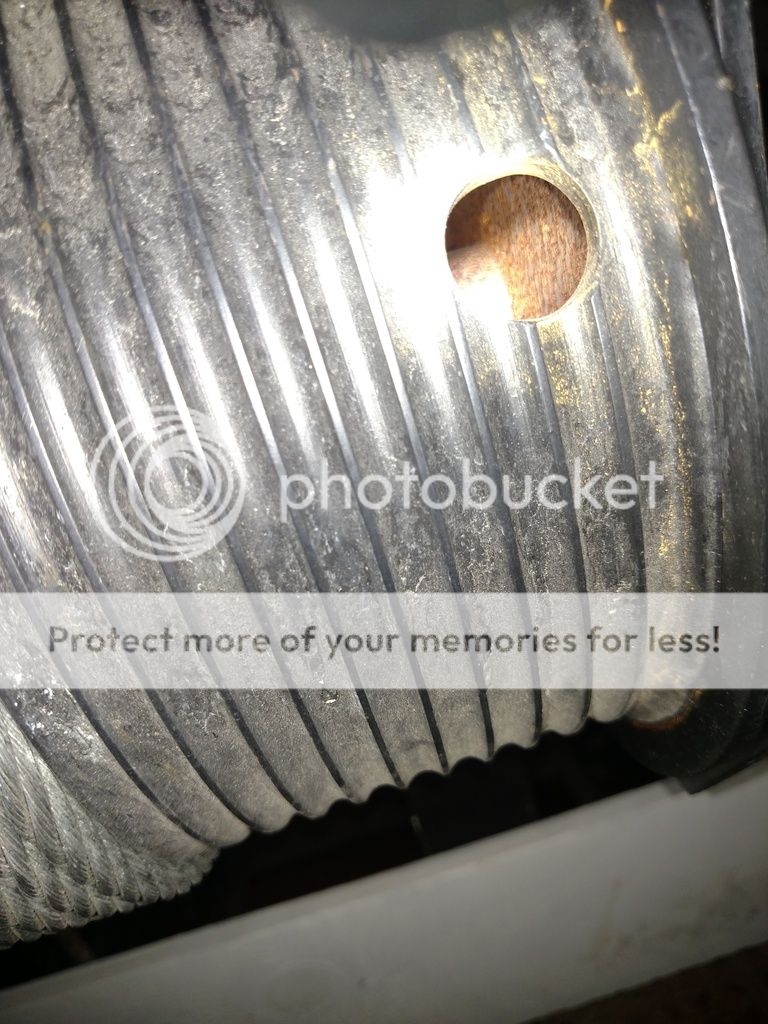
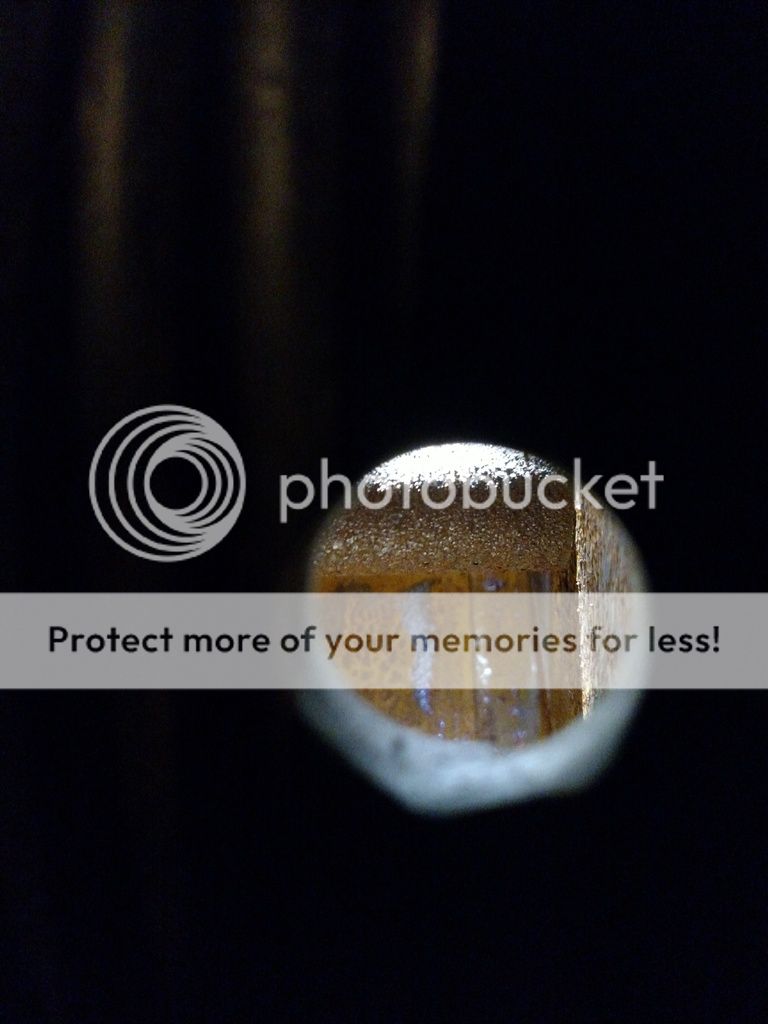