llecount
Member
If you look at the pictures first.. I'll tell you that there's a story behind this, and luckily I had nothing to do with it.. I just unfortunately inherited this disaster.
Long story short, my predcesser here decided to re-route all of our house's mic inputs and stage returns from our central rack (where the former patchbays were), to the table where the console sits. The method taken to move these lines is one that cannot easily (at all) be un-done, so I am stuck with all my stage lines and FOH mix lines landing here.
So this is where I call to you audio professionals for your advice on this situation.
As you can see in the pictures, I have a rats nest of cables that all lead to mic jacks, or return jacks all over the venue. (42+ mic lines, 16+ returns + FOH mix lines)
This creates problems when trying to patch up our house console for events, as it is often difficult to find the line that you are looking for since they are tangled with several others. (yes they are labeled).
I'd like to find an easier option that would allow me to patch my on stage mic jacks and returns to either a whip that goes to the house console (in the booth), or to my FOH mix panel. In the first picture, you'll see all the empty desk space available.. I'd ideally like to have a patch panel integrated in to that empty space.
What patch bays would you recommend? Pre built, or custom built?
What other ways would you recommend that I attempt to make this mess easier to deal with?
I am open to and greatly appreciate all ideas on this project!
Pictures:
The 2 coils in the picture are my FOH mix lines. Simply put, these lead to the FOH mix position where there is a panel for patching in to the house lines.

This mess are the mic and return lines from the stage (and other places) in the venue.

These are the old patchbays we had in place. I was informed that these were "worn out" and wouldn't make proper connections anylonger. At the time they were removed from service, they were probably 17 years old. We have 6 or 7 of these total, all living in a storage cabinet now.

Long story short, my predcesser here decided to re-route all of our house's mic inputs and stage returns from our central rack (where the former patchbays were), to the table where the console sits. The method taken to move these lines is one that cannot easily (at all) be un-done, so I am stuck with all my stage lines and FOH mix lines landing here.
So this is where I call to you audio professionals for your advice on this situation.
As you can see in the pictures, I have a rats nest of cables that all lead to mic jacks, or return jacks all over the venue. (42+ mic lines, 16+ returns + FOH mix lines)
This creates problems when trying to patch up our house console for events, as it is often difficult to find the line that you are looking for since they are tangled with several others. (yes they are labeled).
I'd like to find an easier option that would allow me to patch my on stage mic jacks and returns to either a whip that goes to the house console (in the booth), or to my FOH mix panel. In the first picture, you'll see all the empty desk space available.. I'd ideally like to have a patch panel integrated in to that empty space.
What patch bays would you recommend? Pre built, or custom built?
What other ways would you recommend that I attempt to make this mess easier to deal with?
I am open to and greatly appreciate all ideas on this project!
Pictures:
The 2 coils in the picture are my FOH mix lines. Simply put, these lead to the FOH mix position where there is a panel for patching in to the house lines.
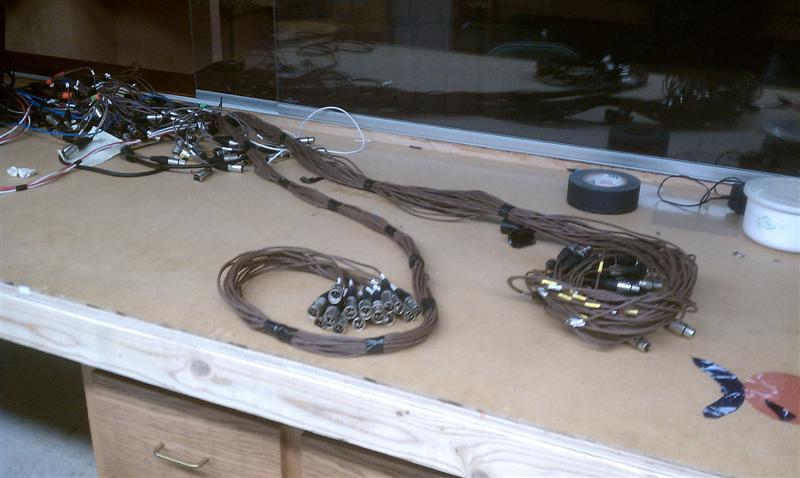
This mess are the mic and return lines from the stage (and other places) in the venue.
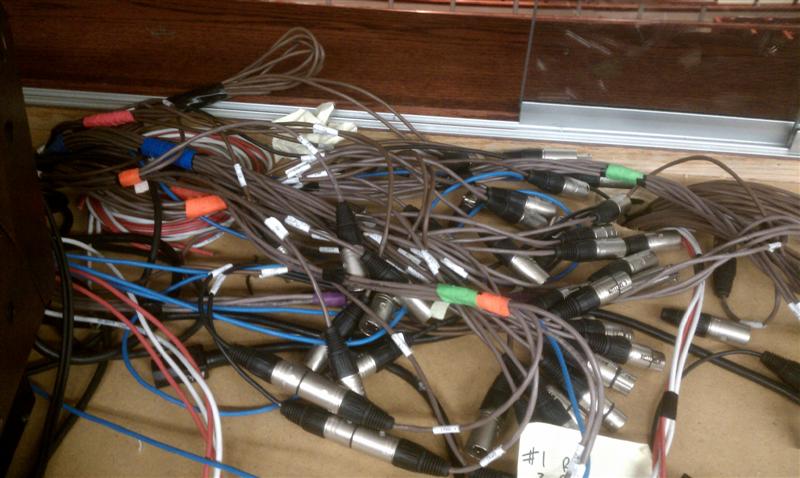
These are the old patchbays we had in place. I was informed that these were "worn out" and wouldn't make proper connections anylonger. At the time they were removed from service, they were probably 17 years old. We have 6 or 7 of these total, all living in a storage cabinet now.
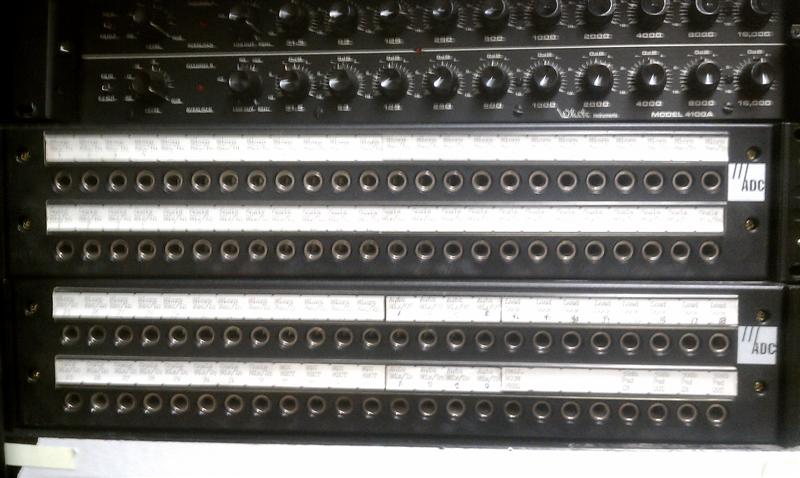